How Professional Packaging Equipment Repair Services Reduce Downtime and Boost Productivity
Expert product packaging maker repair services are crucial in decreasing downtime and improving efficiency through specialized diagnostics and prompt treatments. The effects of such solutions prolong past prompt repair services-- unboxing the wider effect on operational performance reveals critical insights into lasting efficiency methods - packaging machine repair service.
Value of Timely Repairs
Timely repair services of product packaging devices are important for preserving functional efficiency in any kind of manufacturing environment. When equipment breakdowns or breaks down, it can cause significant disturbances in manufacturing lines, resulting in boosted downtime and lost revenue. The longer a packaging machine stays out of compensation, the greater the effect on overall performance, possibly causing delays in fulfilling orders and diminishing client complete satisfaction.
Along with the instant financial implications, postponed repair services can result in much more comprehensive damages to the equipment. Components that are not addressed promptly can deteriorate additionally, needing more expensive repair services or complete substitutes, which could have been prevented via prompt treatment. Moreover, regular upkeep and prompt repair services can enhance the lifespan of product packaging machines, making certain that they run at optimal efficiency degrees.
Investing in professional packaging maker repair work services is necessary for mitigating these threats. An aggressive strategy to repairs not only maintains production routines however likewise fosters a culture of reliability within the organization. By prioritizing prompt repairs, companies can maintain their affordable side, maximize resource allowance, and inevitably improve their profits with boosted operational performance.
Proficiency in Diagnostics
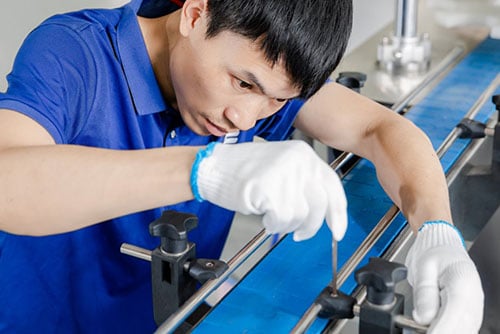
Efficient diagnostics not just help with speedy identification of troubles however likewise boost the general integrity of packaging operations. By performing detailed assessments, professionals can evaluate the health of important parts, making sure that also small irregularities are resolved promptly. This attention to information reduces the risk of unforeseen failures, which can result in costly downtime.
Additionally, specialist diagnostics offer beneficial understandings into operational fads, permitting companies to make educated choices regarding devices upgrades or modifications. By leveraging these understandings, firms can optimize their packaging processes, causing boosted efficiency and productivity. Eventually, purchasing analysis knowledge is necessary for organizations seeking to preserve smooth procedures and promote high standards of quality in their packaging procedures.
Preventive Upkeep Benefits
Preventive upkeep enhances specialist diagnostics by proactively attending to prospective problems prior to they materialize into serious problems. By carrying out an organized preventive upkeep the original source program, firms can considerably decrease the danger of unexpected device failures, therefore lessening pricey downtime. Normal assessments, cleansing, and parts replacement help make certain that product packaging machinery operates at optimum effectiveness.
One of the crucial benefits of preventive maintenance is its capability to expand the life-span of devices. By on a regular basis maintaining equipment, businesses can prevent the worsening results of deterioration that frequently cause major repair work or replacements. packaging machine repair service. This not only saves resources but also boosts the total reliability of production processes
In addition, preventative upkeep contributes to improved safety conditions within the workplace. By recognizing and rectifying potential threats prior to they intensify, companies create a more secure atmosphere for their workers. their website This proactive approach not only shields workers yet also promotes a culture of obligation and alertness.
Custom-made Solution Solutions
Acknowledging the distinct requirements of each business, tailored solution options for product packaging device fixing deal customized strategies that improve functional effectiveness. These services are made to resolve details obstacles faced by different industries, making sure that maker downtime is reduced and productivity is made the most of.
Professional repair work services start with a comprehensive assessment of a company's packaging procedures. By understanding the certain machinery entailed and the demands of the production setting, service technicians can create a personalized maintenance and repair work plan. This may consist of specialized training for internal team, the execution of predictive upkeep innovations, or the arrangement of committed support during optimal production times.
Additionally, personalized remedies can integrate flexible solution arrangements that line up with a company's operational routine, allowing for repair services to be done throughout off-peak hours. By prioritizing the special requirements of each business, these bespoke options ensure that repair services are not only reliable however additionally flawlessly integrate right into existing operations.
Inevitably, the focus on modification makes it possible for firms to optimize their product packaging processes, leading to improved integrity and performance of equipment, which is important for maintaining competitive advantage in today's fast-paced market.
Effect on Total Efficiency
Personalized service options not just address specific repair needs however likewise play a substantial function in improving general functional effectiveness. By supplying targeted treatments, specialist product packaging device repair service solutions directly lower the regularity and period of devices failings. This aggressive strategy makes certain that assembly line stay operational, lessening disturbances that can lead to pricey downtime.
Moreover, efficient repair service services add to smoother click to investigate workflows, as well-maintained machinery runs at optimum performance degrees. When equipments work properly, the top quality of packaged items enhances, causing less flaws and less rework. This enhancement not only enhances productivity but also reinforces consumer contentment.
Furthermore, regular upkeep and quick response times from repair specialists foster a society of dependability within the company. Workers can focus on their key jobs instead than bothering with possible devices malfunctions. As a result, the general throughput of the production procedure increases, allowing firms to meet need better.
Eventually, the calculated investment in expert repair services equates to boosted effectiveness across all operational aspects, guaranteeing that services can adjust and flourish in an open market. This harmony between maintenance and performance is important for long-term success.
Final Thought
In conclusion, specialist product packaging machine repair service solutions play an essential role in lessening downtime and improving productivity within producing settings. Timely repair services, expert diagnostics, and precautionary maintenance add to the integrity of devices, while personalized service remedies resolve certain operational demands. The collective impact of these solutions causes improved total efficiency, enabling companies to keep production schedules, support product high quality, and effectively meet market demands. Investing in such solutions inevitably drives continual functional success.
Comments on “Packaging machine repair service for lasting and dependable fixes.”